Así fabrica Alcoa el aluminio primario: con bauxita, alúmina y energía a raudales
ECONOMÍA
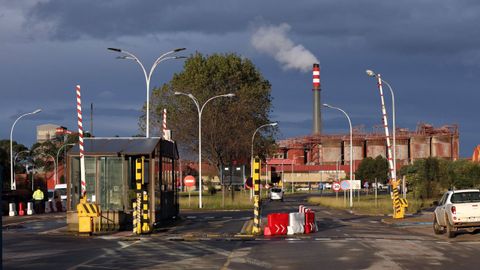
Alcoa es el único fabricante de este metal en España, pero quiere dejar de hacerlo en A Coruña y Avilés
16 ene 2019 . Actualizado a las 05:00 h.Tres plantas de aluminio primario, en A Coruña, Avilés y San Cibrao (Cervo), y una de alúmina, también en San Cibrao, con una plantilla directa conjunta próxima a los 2.000 trabajadores, el 80 % de ellos en Galicia. Así es la multinacional estadounidense Alcoa, la reina del sector, o un monopolio, como la califican los comités de empresa. El grupo opera en España desde hace 21 años, cuando se hizo con los activos de la pública Industria Española del Aluminio (Inespal). Nadie más que él fabrica aluminio primario en el país. Pero, ¿cómo se hace este metal? Pues como se explica a continuación, con datos de la propia compañía.
bauxita, para empezar
De Guinea Conakry a San Cibrao. La fábrica de alúmina de San Cibrao, con una plantilla de 511 empleados, es de Alcoa, pero solo en un 60 %; el resto pertenece a la australiana Alumina Limited. La capacidad de producción suma 1,5 millones de toneladas de alúmina. Se trata de un polvo blanco que se elabora con lo que parece tierra rojiza, la bauxita, que llega en barco procedente de las minas de Guinea Conakry, en África, que también son de Alcoa. De cuatro toneladas de bauxita salen dos de alúmina. Esta planta está conectada al gasoducto, por tanto, el coste de la electricidad no es un lastre. A este último factor se suma una situación coyuntural favorable para los fabricantes de alúmina: el precio de este producto se ha triplicado en los últimos meses por el desabastecimiento provocado por el parón de una gran planta en Brasil. Esto es bueno para esta fábrica gallega, pero malo para las de aluminio, que ahora están perdiendo dinero al incrementarse los costes de producción.
alúmina para continuar
De San Cibrao a San Cibrao, Avilés y A Coruña. La alúmina que se fabrica en la costa lucense se reparte entre las tres plantas de Alcoa que elaboran aluminio primario, en San Cibrao, A Coruña y Avilés. La primera es la mayor de las tres, y con diferencia, y también la más moderna, pues empezó a funcionar en 1981. En ella trabajan 661 empleados y tiene capacidad para producir 234.000 toneladas de aluminio primario. Debido al elevado precio de la alúmina, el año pasado registró pérdidas por importe de casi 54 millones de euros. Pero no está en la picota, como las otras dos.
la electrolisis, vital
Electricidad a borbotones para obtener el metal. Las fábricas de A Coruña y de Avilés son casi gemelas, aunque la primera es tres años más joven (funciona desde 1961). La gallega cuenta con una plantilla de 369 trabajadores y capacidad para producir 87.000 toneladas al año, aunque opera por debajo del 65 %. La asturiana da empleo directo a 317 operarios y es capaz de elaborar 93.000 toneladas, pero funciona también al 65 %. Ambas plantas están equipadas con dos series de electrolisis, que son las que la compañía pretende desmantelar. Son el corazón de las instalaciones. La alúmina se introduce en las cubas, donde se disuelve en un baño de sales de criolita. Es entonces cuando se aplican descargas de electricidad para separar el aluminio del oxígeno. Este proceso requiere cantidades ingentes de energía. Según la compañía, las tres fábricas de aluminio primario consumen un millón de euros al día en electricidad, sin descontar los incentivos que recibe de las arcas públicas para sufragar parte de esos gastos. Pero, entre estos y el sobrecoste de la alúmina, la planta de A Coruña cerró el 2018 con pérdidas que suman 42 millones; 40, en el caso de Avilés, según datos facilitados por la multinacional a los comités de empresa.
Volviendo a la electrolisis, en el interior de las cubas se alcanzan los 950 grados centígrados de temperatura durante el proceso de separación del aluminio del oxígeno. El metal, en estado líquido, se deposita en el fondo y se extrae de ahí por sifón. Estas son las cubas de electrolisis que la multinacional quiere desmantelar. Sin ellas, ya no podrá fabricar más aluminio primario ni en A Coruña ni en Avilés.
a la fundición final
A alearse. La planta de A Coruña cuenta también con hornos de fundición que producen aluminio primario en forma de placas, tochos y lingotes, que vende luego, entre otros, a las gallegas Cortizo, Extrugasa y Exlabesa. También dispone de una planta de pasta Söderberg y electrometalúrgica para hornos eléctricos. En Avilés hay hornos de fundición que producen aleaciones de aluminio en forma de lingotes y tochos, según la compañía. A estas instalaciones llega el aluminio líquido donde se alea para obtener el producto final encargado por los clientes de Alcoa. El metal líquido se introduce en moldes para obtener la forma deseada: puede ser tocho para extrusión, lingote para piezas de fundición o placa para laminación. La multinacional estadounidense quiere quedarse con esta parte final del procesado del aluminio primario, que se fabricaría en otro sitio diferente, pues sin electrolisis, imposible seguir haciéndolo en A Coruña y Avilés.
La multinacional da trabajo directo a 2.000 empleados, el 80 % de ellos en Galicia, en dos plantas en San Cibrao y una en A Coruña