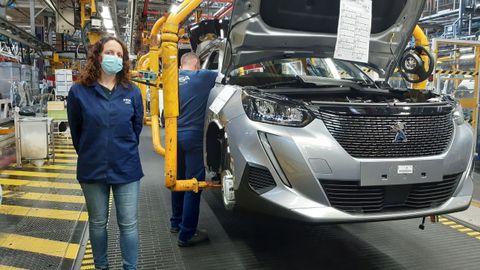
Los ERTE comienzan a hacerse efectivos en miles de trabajadores del sector
14 may 2021 . Actualizado a las 00:35 h.La crisis de los microchips está golpeando con fuerza a la comarca de Vigo. Más de 10.000 trabajadores de la automoción están parados. Se han dejado de fabricar más de 4.600 coches, lo que supone que miles de piezas se han dejado de vender y de trasladar desde las empresas auxiliares hasta la factoría de Balaídos. Esta volverá a funcionar a las 22.00 horas de hoy si no ocurre un nuevo imprevisto en una temporada en la que los sobresaltos son muy frecuentes. Las paradas de producción se van sucediendo por falta de piezas y el gigante automovilístico y sus auxiliares tienen que afrontar como pueden las carencias de piezas por falta de semiconductores.
El grupo Stellantis tiene tres factorías en España, otra en mangual de Portugal y otra en Kenitra en el norte de Marruecos que forman el denominado polo ibérico. Pero en tiempos de escasez, como es el momento actual, por la falta de microchips para la industria, las diferentes plantas de producción tienen que competir y coordinarse para producir coches y que las paradas no les afecten más de la cuenta.
Los sindicatos confirman que ya ha empezado en serio la aplicación de los expedientes de regulación de trabajo temporal tanto en Stellantis como en muchas importantes auxiliares del sector.
La parada de Stellantis tiene un impacto de cerca del 70 % en la industria de la automoción de Vigo, señala Víctor Mariño, de la Central Unitaria de trabajadores el 30 % restante es producción de piezas a la otros fabricantes. Ceaga no ha pormenorizado las paradas en las 200 empresas del sector, pero son muchas. Mariño asegura que en la fábrica apenas hay almacenes, no existe estocaje ni margen de maniobra. Desde que se pide una pieza hasta que llega pueden pasar tres o cuatro horas, a veces hasta ocho.
Si se corta la cadena de suministro, las repercusiones van en cascada. Antes de la crisis del 2008 se preveía mejor el abastecimiento, señala Mariño. Entonces la empresa podía aguantar una semana sin nuevos repuestos porque tenía un almacén suficientemente amplio para albergar las piezas que se consumían en este tiempo. Pero empezaron los recortes en gastos de logística y en el almacenaje para abaratar costes. El just in time funciona solo mientras van bien las cosas y nadie contaba con la pandemia y sus consecuencias.