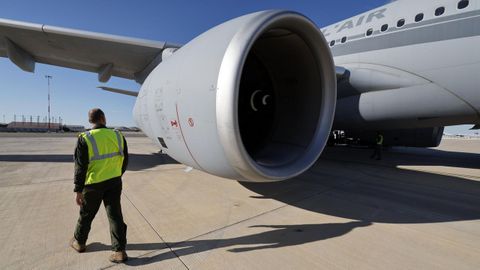
Feuga participa en un proyecto que consiste en introducir sensores digitales en los motores de los aviones para monitorizarlos y detectar daños a tiempo
23 feb 2025 . Actualizado a las 05:00 h.Existe un nexo común entre el proveedor francés de la industria aeronáutica Safran, el fabricante de fibra óptica alemán FiSens y el gigante belga Comet, especializado en el tratamiento de residuos industriales. Y hay también una vinculación de estos grupos empresariales con la Universidad Técnica de Delf, en los Países Bajos; la de Patrás, en Grecia, o la Fundación Empresa-Universidad Gallega (Feuga). Todos ellos, y alguno más, son miembros del consorcio que ha desarrollado el proyecto Morpho, financiado por la Unión Europea, para crear y testar sensores y componentes inteligentes que mejoran la seguridad y la eficiencia de las palas que se utilizan en los motores de los aviones, pero cuyo uso también es susceptible de ser aplicado en la náutica marina o a los aerogeneradores del sector eólico.
Bajo la coordinación de la Escuela Nacional Superior de Artes y Oficios de París, el proyecto reúne a una decena de socios, entre los que se cuentan fabricantes de equipos aeronáuticos, desarrolladores de software y de sistemas de sensores, así como empresas de tecnología de reciclaje y de control de procesos inteligentes, universidades y organizaciones de investigación de seis países europeos.
El socio gallego en Morpho es Feuga, encargado de la protección intelectual del programa, así como de la organización de las sesiones conjuntas de trabajo y de la difusión de los resultados. Ángela Muñiz, gestora sénior de proyectos europeos de la fundación, destacó la importancia que tiene el desarrollo de este proyecto, con las pruebas realizadas en un «demostrador», la ala de un avión, pero utilizando también un «gemelo híbrido digital» para aplicar modelos de inteligencia artificial que contribuyeron a ganar eficiencia en la fabricación de las piezas y anticipar su posible desgaste.
Posibilidad de detectar daños en las piezas en tiempo real
El programa de innovación llevado a cabo consiste en utilizar sensores de fibra óptica y kits eléctricos en áreas difícil de alcanzar del motor de un aeroplano. Eso permite detectar cualquier daño en las piezas en tiempo real, contribuye a anticipar fallos y hace más eficientes los mantenimientos periódicos que tiene que realizar los aparatos, lo que lleva aparejado una reducción de los costes de explotación, logrando, además, una mejora en la seguridad.
Es más, los sensores no van colocados sobre las palas de los motores, sino que se integran en ellas durante el proceso de fabricación. Este consiste en un modelo de transferencia por resina en moldes cerrados mecánicamente, que después se mezcla con fibra de carbono, y es ahí donde se incorporan los sensores.
Por cada ciclo de producción de las piezas, el proyecto logró una reducción del 50 % en el tiempo empleado, lo que agilizó el proceso de fabricación, además de su eficiencia debido a la reducción de los costes.
Financiación de la UE para desarrollar el proyecto en 3,5 años
El proyecto Morpho nació, como dice su nomenclatura en inglés, Manufacturing, Overhaul, Repair for Prognosis Health Overreach, para analizar la fabricación, revisión y reparación por pronóstico de salud de los materiales. Su puesta en marcha fue financiada a través del programa Horizonte 2020 de la Unión Europea (UE) para implementarlo durante 3,5 años. La investigación arrancó en el año 2021 y concluyó el pasado mes de enero con la sesión final en la que se extrajeron las conclusiones.
El hecho de que grupos industriales como Safran Tech, FiSens o Synthesites se embarcaran en el mismo prueba el interés que tiene para la fabricación de estructuras inteligentes para la navegación aérea. Que también se implicara la belga Comet, especializada en la economía circular y reciclaje de metales, supone una apuesta por la sostenibilidad en el uso de los materiales, interés muy relevante para la aplicación de esta tecnología en Galicia, pues permite reutilizar todas las resinas y fibras de carbono.
«Poder reutilizar la fibra de carbono abre la puerta a múltiples usos industriales»
Ángela Muñiz, gestora sénior de los proyectos europeos de la Fundación Empresa-Universidad Gallega (Feuga), estuvo muy cerca de desarrollo del proyecto Morpho y considera que una de las partes más importantes es la del reciclaje de los materiales. «Poder reutilizar la fibra de carbono es un gran avance que abre la puerta a múltiples usos industriales», señala, reduciendo así el impacto ambiental y las emisiones.
Y es que los polímeros reforzados con fibra de carbono, que reducen el peso de los aviones, son muy difíciles de reciclar. En cambio, mediante un proceso de pirólisis, seguido de otros de oxidación probado por el grupo Comet, se pudo recuperar la fibra de carbono «con características muy similares al carbono original», apunta Ángela Muñiz. En la recuperación solo se pierde el 10 % de la dureza y las propiedades básicas del carbono.
La merma que sufre el material en el reciclado es muy pequeña. Quizás no sea ya la fibra de carbono más adecuada para usar en la industria aeronáutica, pero sí que se le abren otras muchas posibilidades de uso muy extendido en Galicia.
Por enumerar solo algunas, como apunta la representante de Feuga, estaría el uso de este tipo de materiales en la fabricación de componentes para los aerogeneradores que pueblan los parques eólicos. O también para las piezas que se emplean en la construcción naval o incluso en la industria de la automoción.